Understanding Rotary Screen Printing Technology
How Rotary Screen Printers Work
The rotary screen printing process is a pivotal method in textile printing, utilizing a cylindrical screen to deliver ink onto substrates. At its core, this method involves the etching of designs onto a mesh cylinder, which rotates as material passes beneath it. During printing, ink is flooded inside the screen, while a squeegee presses it precisely through the perforations onto the fabric. This continuous rotation ensures consistent ink application, facilitating multi-color registration via distinct screens for each color. Known for its efficiency, rotary screen printing surpasses traditional flatbed methods in speed and volume, rendering it exceptionally suitable for large-scale productions.
Key Components of Rotary Screen Printing Machines
A rotary screen printing machine consists of several key components that enhance its performance and quality. The pivotal elements include:
-
Rotary Screen: This cylindrical screen bears the etched design, continuously rotating to transfer ink accurately.
-
Squeegee: Positioned inside the screen, this rubber blade pushes ink through the mesh pores to ensure a dense application.
-
Ink Tray: This manages the ink flow and maintains the desirable viscosity, crucial for consistent print quality.
-
Drying System: Following ink application, the drying system cures the fabrics, setting the inks permanently.
Technological advancements have further refined these components, providing enhanced durability and precision that elevate output quality. The integration of innovative materials and mechanisms has been pivotal in improving the longevity and functionality of rotary screen printing machines.
Comparison with Flatbed and Digital Printing Methods
Rotary screen printing distinguishes itself from both flatbed and digital printing through several comparative advantages. While flatbed printing permits intricate designs, the rotary system excels in high-speed production and vibrant color rendering. Digital printing offers unmatched detail, but rotary methods are preferred for large runs due to cost-effectiveness and color consistency. In scenarios demanding precise color accuracy or significant quantities, rotary screen printing proves ideal. Moreover, statistical analyses often show rotary techniques to have lower cost-per-unit and reduced production timelines compared to their counterparts, particularly in industrial-scale operations.
In summary, each method holds specific strengths and weaknesses, making the choice dependent on project requirements regarding speed, detail precision, and production volume.
Cost-Effective Advantages for Graphic Studios
Lower Operational Costs vs. Traditional Methods
Rotary screen printing offers significant cost savings over traditional methods by reducing setup time and labor costs. This method allows for quicker setup and less labor-intensive processes, which directly translates into financial benefits. Studies have shown that rotary screen printing can lower operation costs significantly due to its efficiency in handling large volumes. According to industry reports, the economies of scale achieved through this technology further reduce the overall expenditure, making it an attractive choice for graphic studios focused on high-volume printing.
High-Speed Production for Bulk Orders
The high-speed capabilities of rotary screen printing make it ideal for managing bulk orders effectively. Unlike traditional methods, which can be time-consuming, rotary screen printing allows for continuous production through its rotating cylindrical screens. Expert insights highlight that it facilitates enormous outputs with remarkable speed, with benchmarks indicating that it doubles or even triples the production speed compared to other methods. This attribute is particularly beneficial during peak seasonal demands, where rapid fulfillment of large orders is critical for maintaining customer satisfaction and competitive edge.
Reduced Ink Waste and Maintenance Expenses
Rotary screen printing minimizes ink waste through precise application techniques, optimizing the utilization of ink and significantly reducing excess. Compared to flatbed printing, studies indicate a notable reduction in ink usage, resulting in both environmental and cost benefits. Moreover, rotary screen printers generally require fewer repairs and upkeep than their traditional counterparts, thus decreasing maintenance expenses. Their robust design and technological advancements ensure longevity and reduce the frequency of downtime, providing a dependable and economical solution for ongoing printing needs.
Applications in High-Quality Graphic Printing
Vibrant Textile and Apparel Designs
Rotary screen printing stands out when it comes to achieving vibrant colors and intricate designs on textiles. This technique allows for seamless color transitions and detailed patterns, making it a popular choice for textile printing in the fashion industry. Brands like Nike and Adidas have embraced rotary printing to add vivid and visually appealing designs to their apparel. Rotary screen printing is versatile, handling a variety of fabrics such as cotton, polyester, and silk, enabling a wide range of applications from casual wear to high-fashion pieces.
Durable Prints for Promotional Merchandise
Rotary screen printing excels in providing durable and weather-resistant prints, ideal for promotional items. This technique uses specialized inks that withstand environmental factors, ensuring the longevity of print quality. Case studies show companies like PepsiCo leveraging rotary prints for promotional merchandise, which remains vibrant and intact over time. The ink technology, with its enhanced bonding properties, contributes significantly to the durability of these items.
Custom Studio Artwork on Diverse Materials
The capability of rotary screen printing to work on diverse materials elevates its application in custom studio artwork. This method effectively prints on different substrates, including plastics, wood, and metal, offering artists the flexibility to explore diverse creative possibilities. For instance, artists have utilized rotary techniques to produce detailed designs on custom skateboards and decorative wooden panels. The artistic freedom and customizable options provided by rotary screen printing make it a favored choice for unique and complex projects.
US2-8M Rotary Screen Printer: Studio-Ready Performance
Versatile Printing for Complex Shapes
The US2-8M Rotary Screen Printer is designed to offer versatile printing solutions for various complex shapes and textures. It is particularly beneficial for studios aiming to enhance creativity and achieve stunning results across diverse substrates. The adaptability of the US2-8M to various forms, such as cylindrical, elliptical, or conical products, showcases its innovative uses in different printing requirements. Studio owners commend the machine for its flexibility and the creative freedom it affords them in their projects. These testimonials highlight the printer's ability to manage complex shapes efficiently, thereby expanding artistic possibilities.
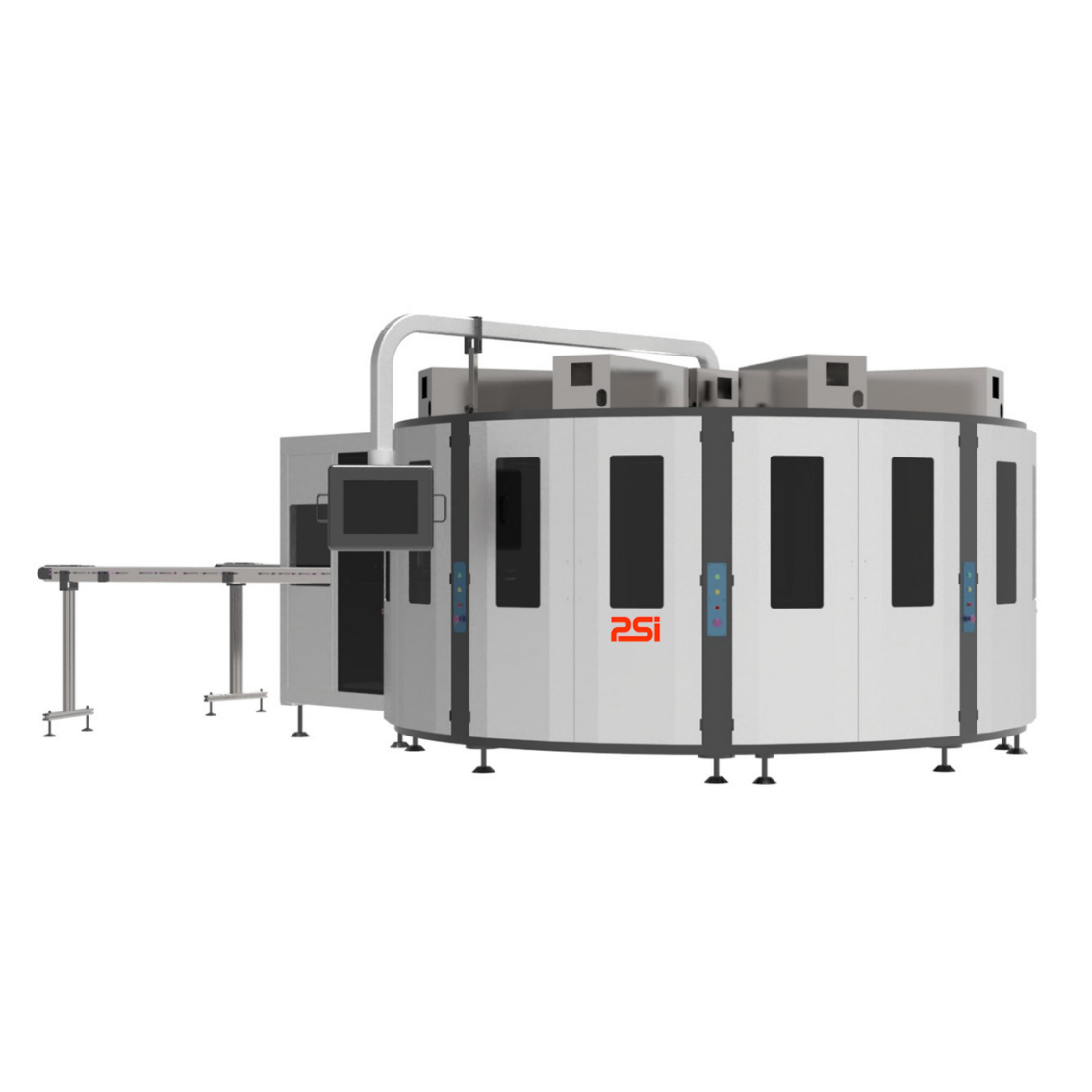
US2-8M Rotary Screen Printer
This model is crafted to print on square, cylindrical, elliptical, and conical products, including bottles, jars, tubes, and cups. Suitable materials include glass, plastic, and metal, boasting high-speed output efficiencies and adaptable UV power sources.
Technical Specifications and Output Efficiency
The US2-8M offers superior technical specifications that cater to the needs of graphic studios. Featuring a maximum printing diameter of up to 100mm and supporting a print stroke of 300-350 mm, it is tailored for various printing demands. Its operational footprint is compact enough for smooth integration into studio environments. With a high output rate of 40-60 pieces per minute, the machine exemplifies efficiency in production processes, making it a preferred choice for high-volume graphic studios. User reviews often underscore its reliability and precision in producing quality prints quickly, affirming its effectiveness in a competitive printing landscape.
UV Ink Compatibility for Eco-Friendly Studios
The US2-8M Rotary Screen Printer is compatible with UV ink technology, promoting environmental sustainability in printing processes. This eco-friendly feature significantly reduces volatile organic compound (VOC) emissions and offers energy savings during the curing phase. UV inks enable quicker curing times, further enhancing overall efficiency. Environmental organizations frequently endorse UV technologies for their contribution to reducing ecological impact, endorsing the US2-8M model for studios committed to sustainable practices. Factoring in such eco-conscious advantages makes this printer a compelling option for studios striving for greener solutions.